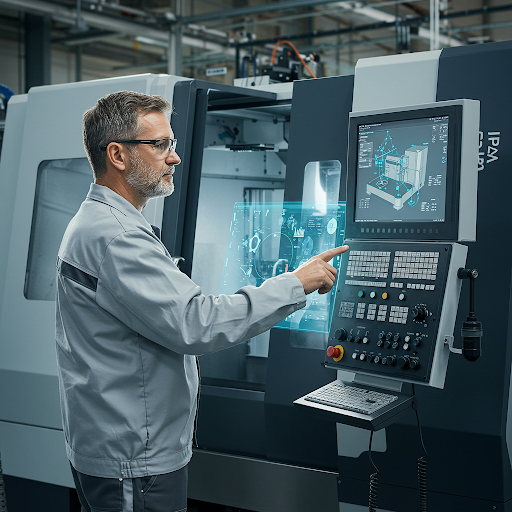
Manufacturing is at a critical crossroads. As competition tightens and customer demands become more complex, manufacturers must adapt rapidly to stay competitive. Yet many still face deeply rooted challenges: equipment downtime, process inefficiencies, unpredictable supply chains, and quality inconsistencies.
Enter Digital Twin technology — a powerful tool that’s helping manufacturers move beyond reactive operations into a world of real-time intelligence and predictive optimization. In this article, we’ll explore the most common problems in manufacturing and how digital twins are reshaping the future of the industry.
What Is a Digital Twin?
A digital twin is a dynamic, virtual representation of a physical object, system, or process. It uses real-time data from sensors, IoT devices, and enterprise systems to replicate how things behave in the real world. Think of it as a living model that evolves alongside your equipment, factory floor, or even your entire supply chain.
More than just a simulation, a digital twin integrates real-time monitoring, analytics, and predictive capabilities. It allows you to test scenarios, forecast failures, optimize operations, and improve decision-making — all without touching the physical system.
Key Problems in Manufacturing Today
Let’s take a closer look at the major pain points most manufacturers face:
1. Unplanned Downtime and Maintenance Costs
When a machine breaks down unexpectedly, it doesn’t just stop production — it can delay orders, affect customer relationships, and lead to costly emergency repairs. Traditional maintenance methods (like periodic checks) can’t catch many of these failures early enough.
How Digital Twin Helps:
Digital twins monitor equipment in real time using sensor data (vibration, temperature, pressure, etc.). By applying machine learning and predictive analytics, they forecast when parts are likely to fail and trigger alerts ahead of time. This enables predictive maintenance, reducing downtime and extending equipment life.
2. Lack of Real-Time Operational Visibility
Manufacturing often involves many systems (PLCs, SCADA, ERP, MES) that don’t always communicate effectively. This leads to blind spots where critical data is delayed, disconnected, or difficult to act upon.
How Digital Twin Helps:
A digital twin unifies data from multiple sources into a central, real-time model. Operators and managers get a 360-degree view of operations — from machine status to product flow. This transparency enables quicker decisions, faster troubleshooting, and better coordination between teams.
3. Inefficient Production Planning and Resource Use
Without accurate forecasting and flexible planning, manufacturers often struggle with overproduction, underutilized machines, bottlenecks, or late deliveries.
How Digital Twin Helps:
Digital twins can simulate entire production processes before anything is physically changed. Manufacturers can test different production schedules, line configurations, or what-if scenarios. This reduces trial-and-error on the floor and improves overall efficiency and agility.
4. Quality Control and Product Defects
Defects can result from inconsistent process parameters, human error, environmental changes, or worn-out machinery. Finding and fixing the root cause often takes time — and money.
How Digital Twin Helps:
Digital twins continuously compare actual operating conditions with ideal setpoints. When a deviation occurs, the system can trace it back to a specific step, machine, or condition. This accelerates root cause analysis and improves both process control and product consistency.
5. High Energy Consumption and Sustainability Challenges
Energy is one of the highest operational costs in manufacturing. Yet many plants don’t have the tools to monitor and optimize energy usage at a granular level.
How Digital Twin Helps:
Digital twins track energy consumption in real time, down to specific machines and operations. With advanced analytics, they help identify inefficiencies, suggest improvements, and simulate energy-saving strategies — all of which support sustainability goals and cost reduction.
6. Workforce Skills Gap and Knowledge Transfer
As experienced workers retire, manufacturers risk losing tribal knowledge — the unwritten understanding of processes, equipment quirks, and troubleshooting methods.
How Digital Twin Helps:
Digital twins capture operational knowledge in a digital form, turning it into a shareable, visual, and interactive resource. Newer employees can use these models for training, simulation, and on-the-job support — accelerating their learning curve and reducing dependency on manual oversight.
Real-World Use Case Example
Let’s say a small manufacturing plant installs IoT sensors on its CNC machines and connects them to a digital twin platform. The digital twin collects data on spindle temperature, vibration, feed rate, and tool wear.
Over time, the system learns patterns and predicts tool degradation. The maintenance team receives early alerts, preventing crashes. Meanwhile, the production planner uses the digital twin to simulate job schedules based on machine health, material availability, and customer deadlines. The result? Higher uptime, fewer defects, and improved delivery performance — all with better visibility.
The Future of Manufacturing Is Digital
Digital twin technology is not just a buzzword; it’s a transformative approach to solving real manufacturing problems. Whether you’re running a small factory or a large enterprise, adopting digital twins can offer measurable ROI in the form of:
- Reduced downtime and maintenance costs
- Improved product quality and consistency
- More efficient resource utilization
- Better decision-making with real-time data
- Increased flexibility and resilience
Final Thoughts
The manufacturing world is undergoing a digital revolution, and digital twins are at the heart of it. By bridging the physical and digital, they empower manufacturers to predict, optimize, and innovate like never before.
If you haven’t explored how digital twin technology can benefit your operations, now is the time. Start small — monitor a single machine, simulate one process — and scale as you go. The insight and efficiency you gain might just be the competitive edge your business needs.
Leave a Reply